Setting the Standard for
Offshore Protection
Originally operated in the Hutton field of the North Sea, the Hutton TLP (Tension Leg Platform) was the world’s first platform of its kind.
Constructed by ConocoPhillips in 1982, this structure employed 16 steel tethers instead of the traditional underwater framework, revolutionizing offshore engineering.
- Initial Service Life: Designed for 20 years but exceeded expectations.
- Inspection Highlights:
· 2011: After nearly 30 years, Interzone 1000 was in excellent condition, even in high-impact areas.
· 2022: Confirmed compliance with ISO 24656 standards, demonstrating industry-leading corrosion protection.
Inspection Highlights
- Visual Integrity: No breakdown, cracks, or defects detected, even under magnification.
- Adhesion Strength: Adhesion tests revealed a performance range of 11-13 Mpa, exceeding industry standards.
- Barrier Protection: Electrochemical Impedance Spectroscopy (EIS) confirmed the coating continues to act as an effective barrier, maintaining structural integrity.
Proven Technology for Offshore Applications
Andreas Hoyer, AkzoNobel’s Global Energy Key Account Manager, shared:
“The performance of Interzone 1000 highlights why it’s trusted for offshore assets. Its formulation ensures proven, long-lasting protection, making it the coating of choice for oil, gas, and renewable energy projects.”
Future Applications in Offshore Energy
As the offshore wind energy industry grows, Interzone 1000 provides reliable protection and supports long-term performance goals for owners, engineers, and specifiers. Its application ensures:
- Durability in extreme environments.
- Safety and efficiency during fabrication and application.
- Consistent performance aligned with lifetime expectations.
Project Summary
Dive into the full study to uncover detailed findings, third-party test data, and insights from the Hutton TLP case study.
- Focus Product: Interzone 1000
- Year of Project: 1982
- Project Size: 40,000 litres
Reflecting on the Hutton TLP’s 40-year performance, Interzone 1000 remains the trusted choice for offshore protection. After decommissioning, the structure was moored in Scotland and dismantled at Queen’s Dock in the Port of Cromarty Firth, showcasing the enduring quality of AkzoNobel’s coating technology.
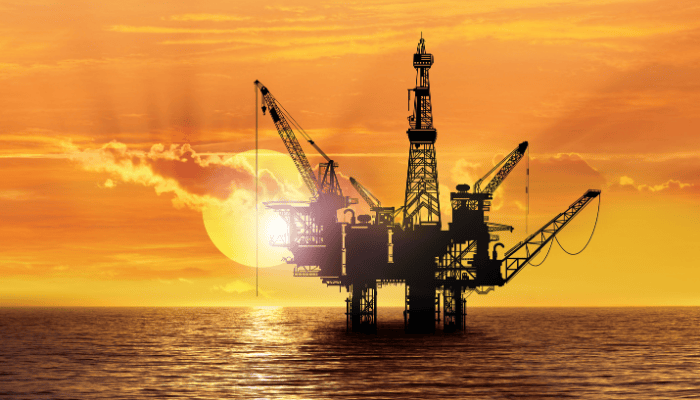
Proven Solutions for Offshore Success
We’re proud to deliver coating systems that go beyond protection—ensuring longevity, efficiency, and safety in the most demanding environments.
Contact us
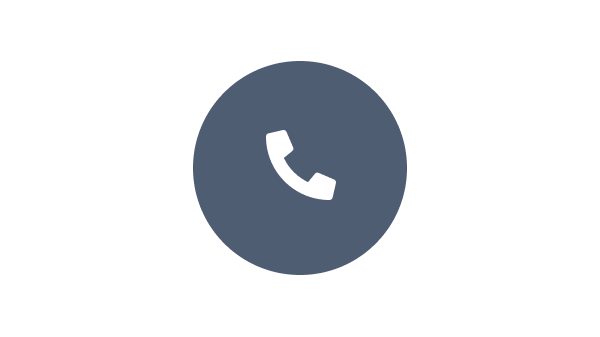
We are here to help
Our global team of technical and sales experts are available to provide you with the help and support that you need.
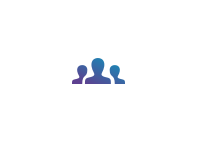
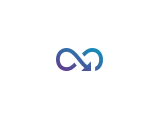
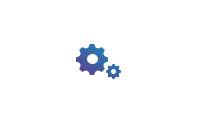